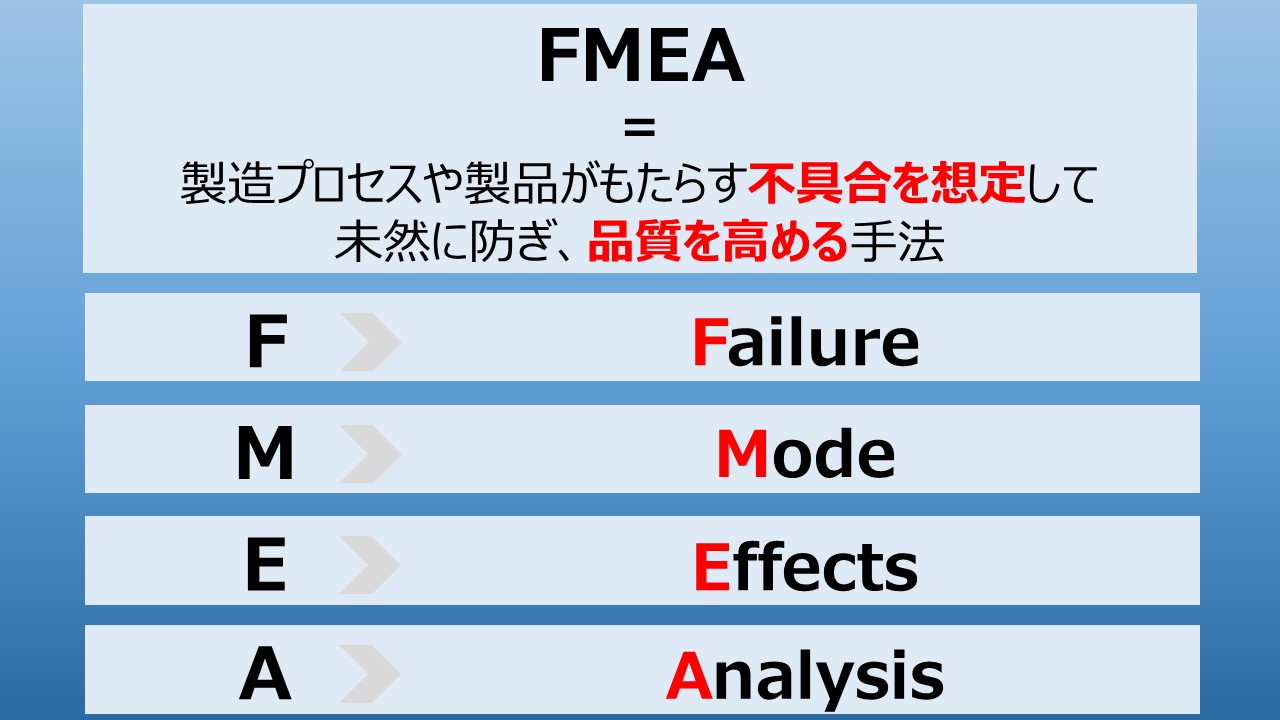
製造業に勤めている人であれば一度は聞いたことある言葉が「FMEA」です。
FMEAとはリスク管理の一つであり、FMEAは製造業以外でも使用できるでしょう。
この記事ではFMEAを知らない方に向けてFMEAの概要とFMEAで聞く重要性や故障モードについて解説します。
FMEAを知らない方、製造業に勤めている方はぜひ本記事を最後まで読んでみてください。
目次
FMEAとは?
FMEAとは「Failure Mode and Effects Analysis」の略であり、「故障モード影響解析」という意味です。
製造プロセスや製品がもたらす不具合を想定して未然に防ぎ、品質を高める手法です。
どういった問題があるのか現状把握をして、対策を立てることであらゆる被害から守れます。
FMEAはあらゆる業務に使用されている手法であり設計段階では設計FMEA、作業段階では作業FMEAと言われます。
工程FMEAと作業FMEA、設計FMEAといったものは全てFMEAの考え方を適用したものです。
FMEAの根本としてトラブルを未然に防ぎ、品質の信頼性を高めるといった目的があります。
FMEAはアメリカ軍が発祥
FMEAは1940年代にアメリカ軍で導入されたのが始まりです。
その後は宇宙開発分野で応用されたり、自動車業界で応用されたりとさまざまな分野で取り入れられています。
故障モードとは?
故障モードとは、摩耗・断線・劣化などによって製品が故障することです。
FMEAを導入する際には、設備や人、方法や環境の変化によって起こると想定される不具合を検討します。
社員の教育ができておらず起きた不具合は、故障モードとして位置付けられます。
工程FMEAの重要性
工程FMEAとは工程にFMEAを当てはめたもので、別名PFMEAとも呼ばれます。
工程FMEAは一定の品質を保つために重要なものです。
製造に必要な作業や設備に不具合がなければ製品の品質は一定に保てるでしょう。
しかし人手不足や設備に不具合が生じれば品質の維持は難しくなります。
つまり品質管理を徹底するためにはトラブルへの備えが必要ということです。
それらを実現化するのが工程FMEAです。
製造工程で起こるトラブルを全て想定することはできませんが、頻繁に起こるトラブルや考えられるトラブルも多くあります。
非日常、経年劣化、非定常などあらゆる場面で起こると想定されるトラブルに対して、常に備えをしておきましょう。
不具合の原因を故障モード・故障モードの影響を加味してトラブルを予防するのがFMEAの考え方です。
工程FMEAの導入と実施方法は?
工程FMEAは以下の手順で導入をします。
- 工程ごとに作業を分類し、さらに動作レベルで細かく分類する
- 各動作で想定されるミスを考え、故障モードの選定
- 故障モードに付随する項目を分析・評価
- 改善案を作成・実行
検討対象を決める
FMEAを導入する前に真っ先にすることがFMEAフォーマットの用意です。
書式については特に決まっていないため、自分が使いやすいと思った書式を使用するようにしましょう。
一般的に記載されている項目は以下の通りです。
- 工程
- 作業項目
- 作業の詳細
- 想定されるミス
- 故障モード
- 故障による影響
- 影響はどのくらいか?
- 故障の発生原因
- 発生頻度
- 故障の検出方法
- 検出度
- RPM
などです。
作業を大きく括り分けて分類し、記入は細かく行います。
さらに動作内の細かい動作を洗い出し、具体的作業を記入します。
故障モードの決定
「想定されるミス」「故障モード」の項目を埋めていきます。
たとえば「部品が緩んでいる」であればミス、「基盤不具合」であれば故障モードといったものです。
これらを細かく記入しましょう。
この際には故障モードのみを考え、設計上のミスなどは除きましょう。
故障モードの分析・評価
このステップでは以下の項目を評価します。
- 故障による影響や影響度
- 故障の発生原因や発生度
- 故障の検出方法・検出度
- RPM
影響度は10段階に分けて細かく評価できるようになっています。
まったく機能しなくなるのか、機能しない恐れがあるのか、まったく影響しないのかなど細かく分類されていますので、当てはまるものにチェックをしてください。
なお故障による影響には、具体的にどのような影響を与えるのか細かく記入しましょう。
もしモニターが出力をしなければ「画面に何も表示されない」となります。
発生度
発生度は故障が発生する頻度を意味します。
毎日なのか、1日に1回なのかなど10段階で評価ができます。
10点が一番発生頻度が高く、週に一回以上発生する確率が起きると考えられます。
8点であれば月一回以上です。
評価基準は自社に合ったものとしてください。
故障の発生原因にはなぜミスが起きるのか要因を記入しましょう。
もし動かないのであれば、「異なる部品の見た目の見分けがつかないため」と記入します。
検出の分析と評価について
検出の分析と評価は不具合に対してどのような管理ができているか評価するものです。
どのように管理をしているか、発生を抑えるための管理はどのような施しがされているのかなどです。
不具合の検出率を5段階で評価し、5が一番検出できないもの、1が一番検出できるものとなっています。
5はお客様の手元に製品やサービスが行き、影響を起こしてから分かるものです。
ただし注意点として人間が検出したものは100%とならず、100%と判断して良いのは機会で検出する場合のみです。
RPM
RPMは影響度・発生度・検出度をかけたものです。
これまで評価したそれぞれを掛けたものが、リスクの大きさを表すものとなります。
RPM=影響度×発生度×検出度
改善案の検討と実施
改善に優先度をつけ、高いものから改善案を立案します。
対策部門、期限、改善の提案、勧告と準備を進めます。
最終的にRPMを低下させましょう。
ただし影響度に関しては、成果物が変わらない以上トラブル発生時の影響は変化しないため下げることは不可能です。
改善したものは再度RPNを計算し、100未満になるまで繰り返しましょう。
FMEAを実施して製品の故障を減らす
工程FMEAは製品や製造プロセスがもたらすあらゆるトラブルを想定して未然防止をし、製品や工程の信頼性品質を高めてくれます。
FMEAを導入すればトラブルや不具合の発生頻度を下げることができ、信頼性が上がるでしょう。
適切に評価をし、FMEAを実践して製品の故障を減らしましょう。